Client Overview
Region
Germany
Industry
Power Tool Manufacturing
Challenges
- Siloed Demand & Supply Planning
- Fragmented Forecasting & Production Planning
- Supporting Multiple Factories & Sales Organizations
Results
- Improved End-to-End Visibility
- Faster Issue Resolution
- Better Decision-Making with a Unified Planning Approach
1. Challenge Overview
Siloed Demand & Supply Planning
STIHL’s global subsidiaries and production units operated independent SAP ERP systems, leading to:
- Inconsistent planning processes across 35 sales organizations and 8 production units.
- Lack of real-time collaboration, causing delays in decision-making.
- Time-consuming data validation, preventing planners from focusing on strategic initiatives.
Fragmented Forecasting & Production Planning
Without an integrated system, STIHL faced:
- Uncoordinated demand forecasts, leading to stock imbalances and missed opportunities.
- Disconnected supply constraints, making it difficult to align production schedules with demand fluctuations.
- High manual effort in tracking inventory positions across multiple systems.
Difficulties in Supporting Multiple Factories & Sales Organizations
- Each subsidiary relied on its own planning tools, making it challenging to align global strategies.
- Lack of a single source of truth resulted in inefficient coordination and lost revenue opportunities.
2. Solution
Legacy Planning Systems to SAP IBP Migration & Integration
- Unified Planning Across Subsidiaries – Migrated STIHL from legacy planning systems to SAP IBP, creating a single, integrated planning environment.
- Seamless Data Flow & Process Standardization – Enabled subsidiaries to operate on a common planning platform, ensuring consistency in demand and supply processes.
- Improved Collaboration – Integrated IBP Demand Planning, Supply Planning, and Response Optimization to enhance coordination and decision-making across global operations.
End-to-End Visibility with SAP IBP
- Optimized Demand Planning (IBP S&OP Module) – Integrated forecasting models with accurate syncing market demand insights.
- Constraint Based Supply Planning (Optimizer) – Aligned production capabilities with inventory availability, preventing bottlenecks.
- Response Planning – Enabled planners to adjust supply chain parameters dynamically, responding to disruptions faster.
- Implementation of Supply Chain Explorer
Bottleneck Capacity
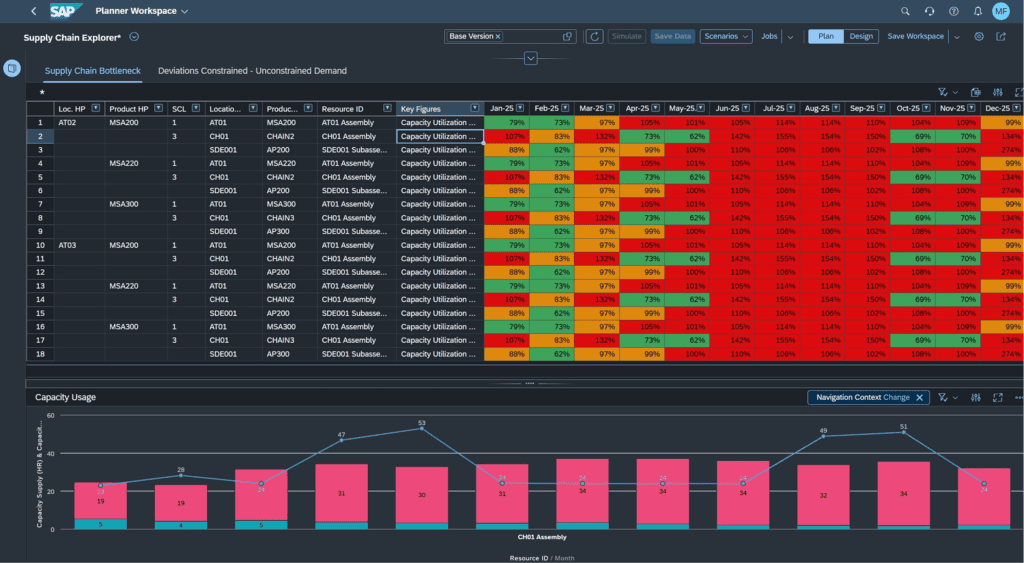
- Identify capacity limits for products and components
- Multi-level, cross-company visibility
- Drill down into supply and usage details
- Navigate in IBP Planner Workspace or Excel Add-On
Demand Deviations

- Visualize supply shortages for products and components
- Multi level, cross company insights
- Drill into cumulative shortage data
- Analyze via IBP Planner Workspace or Excel Add-On
Usage Analysis
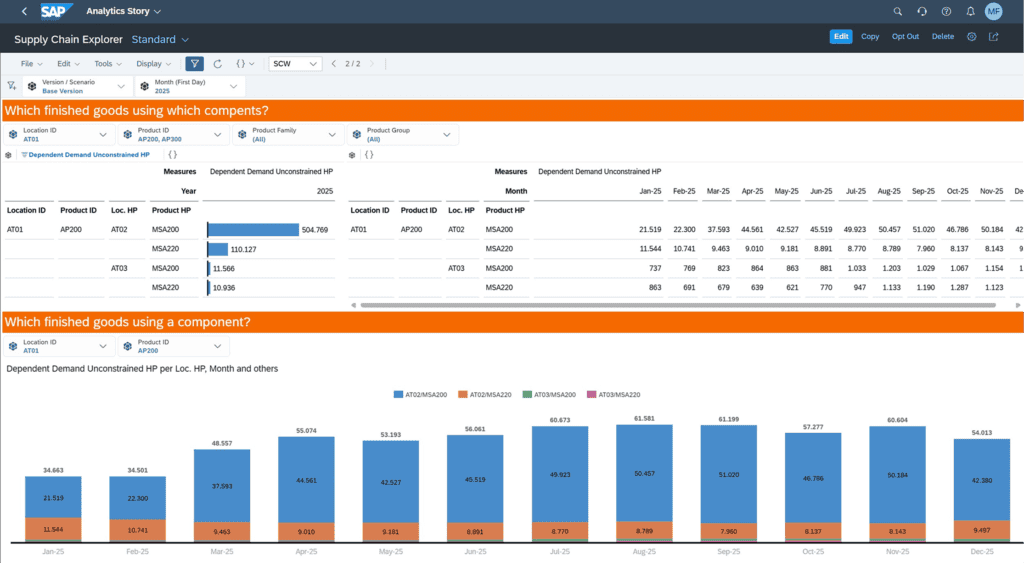
- Analyze component usage by products
- View data at any level, across companies
- Drill into detailed usage data
- Interactively analyze with IBP Analytic Story
Enhanced Coordination Across Factories & Sales Organizations
- Centralized Decision Making – Consolidated 35 sales organizations and 8 factories into a single supply chain view.
- Automated Planning Workflows – Reduced manual effort in data validation and reconciliation across regions.
- Standardized Processes – Established uniform planning procedures, increasing efficiency and reducing lead times.
3. Results
Improved End-to-End Visibility
Connected demand and supply planning across all subsidiaries, providing an accurate, transparent view of inventory, orders, and production constraints.
Faster Issue Resolution
– Planners can now detect and address disruptions proactively, improving supply chain responsiveness.
– Reduction in planning cycle times – STIHL now resolves bottlenecks faster using real-time supply chain analytics.
Better Decision Making with a Unified Planning Approach
– Single Source of Truth – Sales and production teams operate on the same data, leading to better forecasting and resource allocation.
– Network-Wide Optimization – Improved customer service while reducing inventory costs through network planning.
– Time Savings for Planners – Teams now see an updated and accurate impact of changes, allowing them to adjust strategies instantly.
Quick navigation
- Siloed Demand & Supply Planning
- Fragmented Forecasting & Production Planning
- Difficulties in Supporting Multiple Factories
- Legacy Planning Systems to SAP IBP
- End-to-End Visibility with SAP IBP
- Enhanced Coordination
- Improved End-to-End Visibility
- Faster Issue Resolution
- Better Decision Making